This article represents just a snippet from one section of VIVA's full P2 course, which you can join via our All Access membership.
This article focuses on analysing and managing costs. In order to be successful in a modern business environment, businesses need to find ways in which to create value. One way to do that is to reduce their costs. In order to do this, they need to have effective cost management. This article will explore one such technique designed to help businesses manage their costs, called traditional absorption costing.
Absorption Costing & OARs in a Nutshell
Traditional absorption costing was initially designed to help production businesses deal with their production overheads. In particular, what a business would like to do is work out the cost of the products it is producing. Now, when doing this, it's very easy to estimate the direct costs of production (things like direct materials and direct labour). However, it's more difficult when producing a product to say how much that product cost in terms of the overheads per unit. Absorption costing is a method which allows businesses to charge overheads to products produced, which will then allow them to work out an estimated full production cost per unit.
Absorption costing is said to be a simple approach to absorb overheads into cost units. It's certainly much more simple than activity-based costing. What we're trying to do with absorption costing is we're trying to absorb or charge overheads if you like to our cost units, and cost units are nothing more than the products produced, or if you're looking at a service business, the service which is provided. Now, in order to do this, what we first have to do is calculate for each department or cost centre (both terms mean the same thing), what's called an overhead absorption rate, which is often abbreviated to an OAR. An overhead absorption rate is always calculated using a standard calculation, whereby we take the budgeted overheads of that department or cost centre and we divide this by a budgeted level of activity. You'll notice this calculation is based on budgeted figures. This is done at the start of a financial period because this is when a business needs to have a decent understanding of what things like its products are going to cost etc.
What that budgeted level of activity is within the calculation of the overhead absorption rate, actually varies depending on the department under consideration. Therefore, what we look for in questions if we need to determine this is whether or not a department is what we will call machine intensive or labour intensive. If a department is machine intensive, it means the vast majority of the work done within that department is actually automated. It's carried out by equipment, by machinery. Therefore, when we're calculating our overhead absorption rate for that department, we take the budgeted overheads for that department and we divide them by the budgeted machine hours for that department, because machine hours really are a good representation of the work that goes on in that particular part of the factory. However, in some cases, departments will be labour intensive, and that will mean that the vast majority of the work in that department is carried out by human hand. Therefore, if we're calculating an overhead absorption rate for the labour intensive department, we take that department's budget overheads and we divide them by their budgeted labour hours.
So, the key thing is that an overhead absorption rate is calculated based on budgeted figures, and the basis that we use for absorption, i.e. that budgeted level of activity, is usually machine hours or labour hours, depending on whether or not the department is machine or labour intensive.
A Worked Example
Let's take a look at an example for absorption costing and calculating overhead absorption rates.
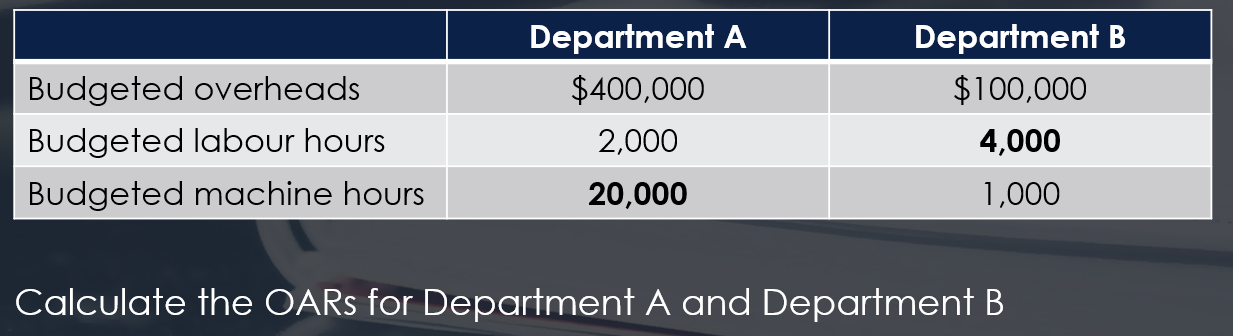
We've got some information here on two departments; we've got department A and department B. Now, what these departments have done is they've estimated what their budgeted overheads for the period are going to be i.e. their indirect costs such as rent, supervisors' salaries etc. Department A has estimated the overheads for the next period are going to be $400,000, and department B has estimated their's will be $100,000. They've also estimated what the labour and machine hours will be for the next period.
Now, if you focus on department A, they've estimated budgeted labour hours of 2,000 and budgeted machine hours of 20,000. Remember, when we're calculating an overhead absorption rate, we need to determine whether or not a department is labour or machine intensive, and you'll see there the 20,000 figure for budgeted machine hours is involved. That means clearly that department A is machine intensive. It means that the vast majority of the work done within this department is carried out by the equipment. So, it's that 20,000 that we'll use as our budgeted level of activity when working out our overhead absorption rate.
On the flip side, department B is clearly a labour intensive department because the estimated or budgeted labour hours for the period are 4,000, whereas they're only expected to use 1,000 machine hours in the next period. So, when we’re working out the overhead absorption rate for department B, we're actually going to use the budgeted level of activity for labour hours, which is 4,000.
So, let's have a look at how that impacts the calculations. Remember, the standard calculation to work out for the overhead absorption rate is:

For department A, that will give us an overhead absorption rate of $20 per machine hour. The budget overheads are $400,000. It’s a machine intensive department so we'll divide that by the 20,000 machine hours which will give us the rate of $20 per machine hour.

What that means is every time a product is expected to use one hour of department A's time, that product will absorb, or if you like, be charged with, $20 of department A’s overheads. We'll see how that transpires in more detail shortly.
To work out the overhead absorption rate for department B, we take the budget overheads of $100,000, and that's a labour intensive department, so our budgeted level of activity is the budgeted labour hours for department B of 4,000.

That gives us an overhead absorption rate of $25 per labour hour, and we now have a mechanism to absorb overheads into the products produced. So, if we had a product that was expected to use one labour hour of department B's time, we would include $25 to cover the cost of department B's overheads.
Absorbing Overheads
Once we've calculated the overhead absorption rates, we can then go through the process of absorbing overheads. This is nothing more than trying to build up an estimated cost of making our products. Let's have a look at how this works.
Overheads are firstly absorbed into cost units, which are just products produced, using the overhead absorption rates. As we said, what we're trying to do here is estimate the full production costs of our products. The full production cost of our products will be made up of the direct costs per unit plus the overhead absorbed per unit. The direct cost per unit will comprise of direct materials, direct labour etc. Add to that the overhead absorbed per unit, which we do using our overhead absorption rates, and we have an estimate for the total production cost at the start of the period. This will give a business the ability to plan more effectively. So, we can do things like set better prices. Once we understand what the full production cost is, we obviously know that if we want to make some money, our price needs to be higher than that. Furthemore, it would allow us to set up budgets which are very, very important for the planning cycle of the business.
Let's Build on our Previous Example
Let's continue our previous example and see how overheads will be absorbed using the overhead absorption rates that we've calculated previously. What we know from the first example is that the overhead absorption rate for department A was $20 per machine hour, and for department B it was $25 per labour hour.
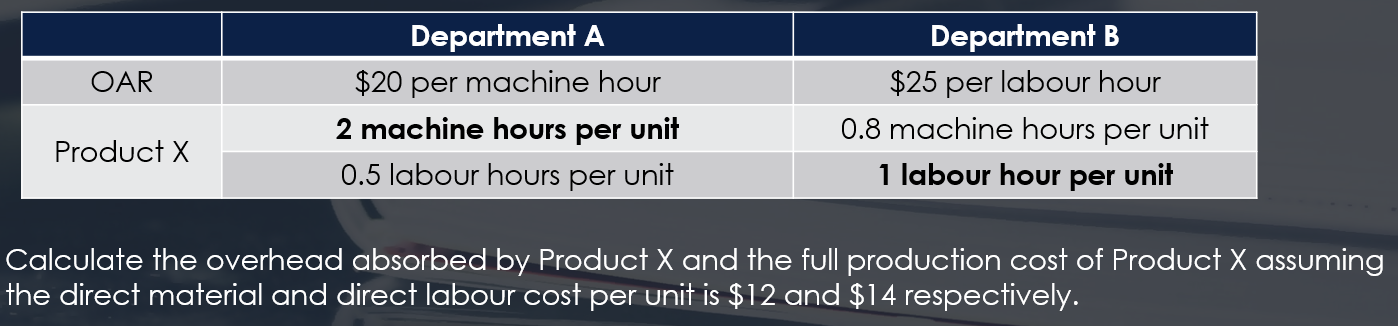
Now, we've got some information here on Product X, and we've got the expected machine and labour times for each of the departments that Product X is expected to use. Product X when it passes through department A is expected to use two machine hours per unit and 0.5 labour hours per unit. It's the two machine hours which is really the important one because we have previously calculated an overhead absorption rate for department A of $20 per machine hour. So, we have to charge or absorb overheads to our products using a machine hour rate. So, it's two machine hours which is important here with respect to Product X and department A.
Moving on to department B. Once again, we've got the expected time in terms of machine hours and labour hours for Product X in department B, but the most important thing is our overhead absorption rate is $25 per labour hour. So, when we're absorbing department B's overheads into Product X, we have to pay attention to the labour hours per unit and in this case, that's one labour hour.
Next we need to calculate the overhead absorbed by Product X and then work out the full production cost having been given the cost for direct materials and direct labour. First of all, to work out the overhead absorbed by Product X with respect to department A overheads, we simply take the overhead absorption rate, which is $20 per machine hour, and we multiply it by the two machine hours that Product X is expected to use when passing through department A. That will give an overhead absorbed of $40 in respect to department A overheads.

On to department B: the overhead absorption rate is $25 per labour hour and Product X is expected to use one labour hour per unit, which gives us an overhead absorbed in respect of department B of $25.

The total production overhead absorbed, therefore, is $65 across the two departments.

We're already told that the expected direct material cost is $12 per unit, and the labour cost is $14 per unit. This allows us to build up the full production cost of Product X. In this case, we've got the $12 and the $14, so we've got $26 in respect of what we will call direct costs, and these are the ones which are easy for us to estimate. But we've now also got the overhead absorption per unit being $65, which gives us a full production cost for Product X of $91.

Over or Under-Absorption
What we know from overhead absorption rates having seen the previous calculations, is the fact that when we work out the OAR, it's based on budgeted figures. We need to do this because at the start of the period we need to have an estimate of what the full production cost per unit is going to be for our products to help us set our prices, to help us plan our budgets etc. However, because the figures are budget figures, there is a chance that our initial estimations were not correct.
There are a couple of different things that happen with an overhead absorption rate. Like we’ve seen previously, they’re used to charge or absorb overheads into products; therefore, we can work out estimated full production costs. What also happens is once we start the financial period, we use them to help us build up an estimate of what our production overheads are going to be. This is a process, again, which we call absorbing overheads. Now, what will happen is each period at the end of that period we'll have to do a little reconciliation exercise. We'll have to compare what we will call our total overheads absorbed to the actual overheads incurred, and there's often a discrepancy here, which we call an over or under absorption. That just means we have to make a slight adjustment to our management accounting records.
So, to work out this over or under absorption, first of all, we work out our overhead absorbed in the period. Here we take our actual hours and we multiply it by the departmental overhead absorption rate. Now again, this would depend on whether or not we had an overhead absorption rate which was based on machine hours or labour hours. If we previously determined that this department was machine intensive, the actual hours would be the actual machine hours worked in the period, and of course, the overhead absorption rate will be a rate per machine hour. A really nice way to think about this overhead absorbed is that this is our estimate of what the production overheads for the period would have been. Every time we worked, in this case, a machine hour, we would have charged a little bit to our production overhead cost account to give us an estimate of what the overheads for the period would be.
So, that's kind of what sits there in our accounting records at the moment. However, once we get to the end of the period, and we've had all our invoices in, we then have a thorough understanding of what we spent on our actual overheads. Then we make this comparison between the overhead absorbed and the actual overheads, and that allows us to work out overhead over or under absorption. In this case, if the overhead absorbed was greater than the actual overheads, we have over absorbed. If you like, we’ve charged a little bit too much and we need to make a correction in our management accounts. On the other hand, if the overhead absorbed was less than the actual overheads, we have under absorbed. In such an instance, we've not quite charged enough. So, once again, we need to make a correction in our management accounts.
Overhead absorbed = actual hours x departmental OARXLess: actual overheadsXOverhead over or under absorptionX or (X)
Taking our Example Further Still: Under or Over Absorption?
Let's have a look at our example in relation to working out over or under absorption.

We're asked to work out the over or under absorption for department A, if the actual machine hours for the period were 21,000 and the actual overheads were $415,000. Now, remember, we've already seen information relating to department A. We determined that it was machine intensive, and we'd already worked out department A's overhead absorption rate being a particular rate per machine hour. So, we have the ability, therefore, to work out the overheads that will be absorbed over the course of this financial period. In order to do this, we take the actual, in this case, machine hours. The actual machine hours worked in the period were 21,000, and we multiply that by department A's overhead absorption rate, which we've worked out previously to be $20 per machine hour. Now, that would give us an overhead absorbed of $420,000, which is what we have in our management accounts at the moment.
However, we then add up all the invoices linked to our overheads and all the payments we've made relating to department A's overheads, and actually, for the period, it only came to $415,000. In this case, the overhead absorbed exceeds the actual overheads by $5,000. So, we have what is called an over absorption. If you like, at the moment what we have in our production overhead cost accounting for department A is $5,000 too high. So, what we'd have to do is just make a slight adjustment to our management accounts to make sure we account for that over absorption.
Summing Things Up
Let's recap as far as absorption costing is concerned. It's a very simple approach to absorb overheads into cost units; very simple in that it's not overly detailed, it's not overly complex. For each department we look at, we need to decide whether they are labour intensive or machine intensive. We work out an overhead absorption rate, and once we've got that we've got a nice simple mechanism to help us work out the estimated full production cost per unit for our products.
If we're going to be comfortable with this area, we need to be comfortable with three main things:
- The calculation of the overhead absorption rate. Remember, this is always budgeted overheads divided by the budgeted activity level. The activity level will either be machine hours if the department is machine intensive or labour hours if the department is labour intensive.
- We then also need to be comfortable with absorbing overheads into cost units. If we want to work out the full production for our products, the direct cost is easy for us to estimate but the overhead absorption rate is going to help us estimate the overhead cost per unit.
- Finally, we need to be comfortable with working out any over or under absorption. Remember to do this, we have worked out the overhead absorbed, which would be the actual hours for the period multiplied by the overhead absorption rate. We then compare that with the actual overheads we incurred and that will give us our over or under absorption, and therefore, highlight any adjustment we need to make to the management accounting system.
You might also want to read: Cost Behaviour and What are Relevant Costs?